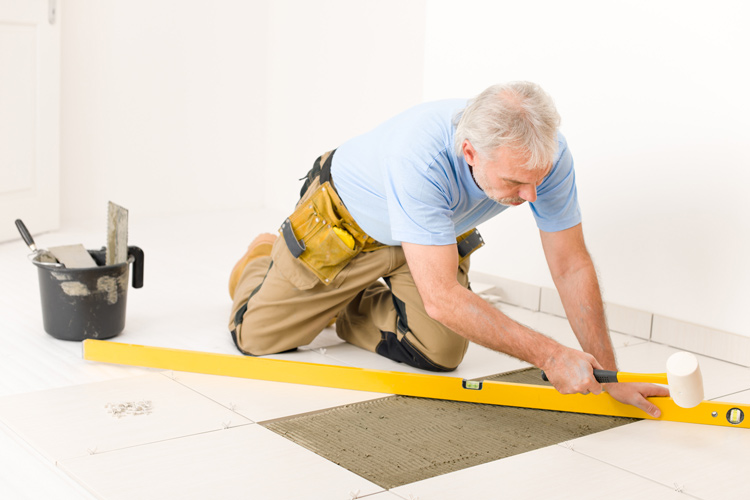
- By w2cadmin
- In Build, Renovation
Steps to Improve Joint Placement in Construction and Renovation
In construction and renovation, joint placement is a critical aspect that determines the longevity and stability of a structure. Whether you’re working on a residential project or a large-scale construction, understanding and improving joint placement can significantly enhance the integrity of the build. This blog outlines key steps to ensure optimal joint placement.
1. Understand Different Joint Types: The first step is to understand the various types of joints used in construction, such as expansion joints, control joints, construction joints, and isolation joints. Each serves a unique purpose, accommodating movement, preventing cracks, and aiding in the overall structural design.
2. Plan Joints in the Design Phase: Effective joint placement begins in the design phase. Work with architects and engineers to identify where joints should be placed based on the structure’s layout, materials used, and expected environmental stresses.
3. Consider Material Properties: Different construction materials expand and contract differently under temperature changes. Understanding the properties of the materials you’re using (concrete, wood, steel, etc.) is crucial for determining the appropriate type and placement of joints.
4. Account for Load Distribution: Joints must be strategically placed to evenly distribute loads and stresses across the structure. This consideration is especially crucial in areas that bear significant weight or are prone to high traffic.
5. Use Proper Spacing: Proper spacing between joints is critical. Over-spacing can lead to cracks and structural weakness, while under-spacing may result in unnecessary material use and increased costs.
6. Implement Expansion Joints in Large Areas: In large concrete slabs or walls, expansion joints are necessary to accommodate movement and prevent cracking. Ensure these are placed at recommended intervals and properly sealed to maintain effectiveness.
7. Precision in Execution: During construction, ensure that the joint placement adheres to the design specifications. Accurate execution is key to the effectiveness of the joints. This might involve the use of specialized tools and techniques.
8. Regular Inspection and Maintenance: Post-construction, regular inspection and maintenance of joints are essential. This helps in early detection of issues like sealant failure or joint widening, allowing for timely repairs.
9. Stay Updated with Industry Standards: Construction standards and best practices evolve constantly. Staying informed about the latest guidelines and technological advancements in joint placement can lead to more efficient and effective practices.
10. Collaborate with Experts: Consulting with structural engineers, architects, and experienced contractors can provide valuable insights into improving joint placement in specific projects.
Joint placement is a nuanced aspect of construction and renovation that requires careful planning, precise execution, and ongoing maintenance. By following these steps and prioritizing joint placement, you can significantly enhance the structural integrity, longevity, and functionality of your projects.
Disclaimer: This blog post provides general guidance on joint placement in construction and renovation. For project-specific advice, always consult with a professional engineer or architect.